Search for articles or browse our knowledge portal by topic.
Structural Steel Coatings
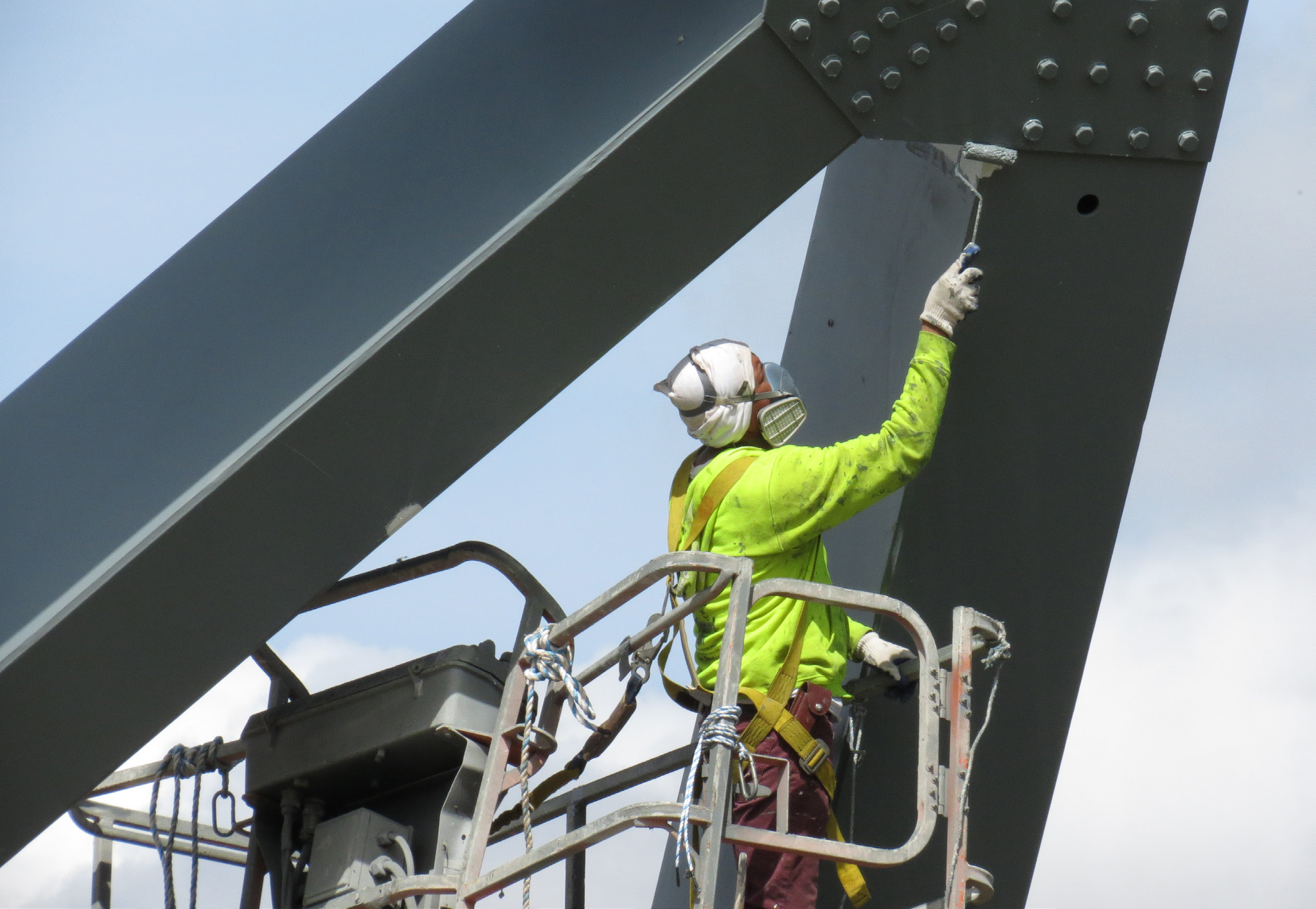
Maintenance painting is KYTC’s most common bridge preservation action. Many highway components undergo maintenance painting, including bridges, sign structures, and guardrails. This form of painting protects a variety of highway materials, including steel (the most common use), reinforced concrete, and wood.
On bridges, the main justification for maintenance painting is to protect structural steel against corrosion. Steel elements corrode when they are exposed to atmospheric moisture; corrosion is also accelerated by the presence of soluble (deicing) salts. Corrosion results in the loss of the load-bearing section of structural steel elements, thereby weakening them. When this occurs, the repair or replacement of expensive structural elements is often required. Another function of maintenance painting is to enhance bridge aesthetics. Consult the Kentucky Standard Specifications for Road and Bridge Construction for a listing of available approved colors.
Maintenance forces can select from a variety of techniques to perform maintenance painting. For example, bridge maintenance painting may entail removing existing coatings and then applying new ones (i.e., removal and replacement). Another technique is localized repair, which is accomplished by cleaning and repainting specific areas, such as beam ends under joints (zone painting), or locations where existing coatings have failed (spot painting). Coatings in a relatively good condition can be rehabilitated by repairing defective areas and painting additional coats over the existing coat (overcoating). KYTC currently relies primarily on removal and replacement for all bridge maintenance painting projects.
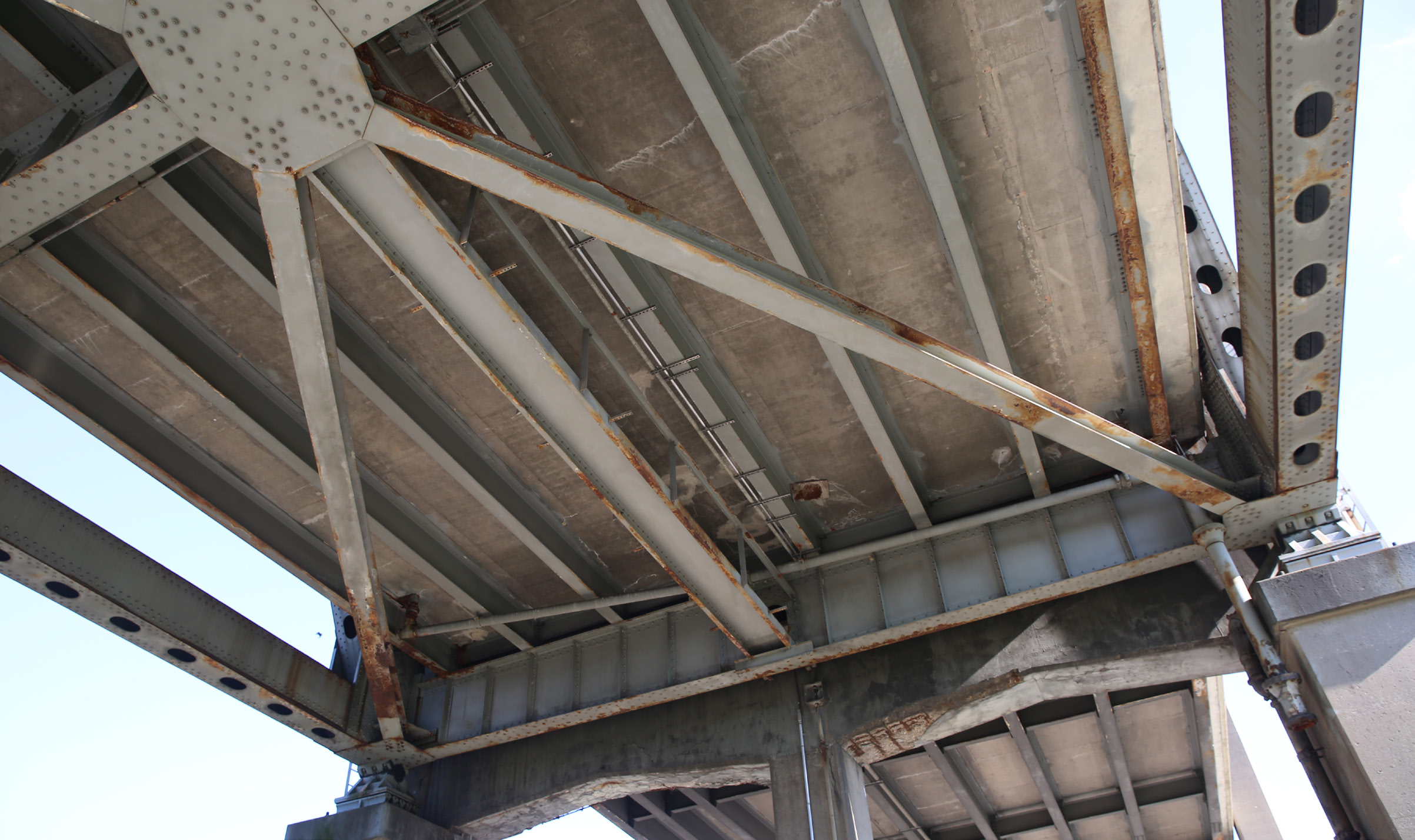
The full definitions for terms included in this article (listed below) can be found in the HKP Glossary.
• Blast Cleaning
• Bresle Patch Test
• Categorical Exclusion
• Chalking
• Coating
• Disbondment
• Fascia Intermediate Coat
• Primer Coat
• Proposal-Type Bid Package
• Top Coat
To ensure good performance, a coating should be applied to uncontaminated (i.e., clean) steel substrates that have been properly abraded. Applying coatings to clean steel helps to achieve proper adhesion. Before a coating is applied, remove existing oils, diesel fumes, tar, or other hydrocarbon residues from existing substrates. These materials can be removed by wiping substrates with solvent-soaked rags or washing them with a detergent.
For removal and replacement painting, KYTC specifies a form of surface preparation that incorporates dry abrasive blast cleaning. This removes all existing paint and dry residues such as rust and dust. Blast cleaning roughens steel substrates, which increases their effective surface areas and enhances adhesion of the primer coat.
A system consisting of an air compressor, blast pot, air lines, and blast nozzle is used to perform blast cleaning. The air compressor generates a stream of high-velocity air in a line attached to the blast pot. Abrasive media (e.g., granite, coal slag particles, recyclable steel shot/grit) are injected into the air lines from the blast pot and carried at high speeds through the lines to the blast nozzle. An operator points the nozzle at the structural steel to be cleaned. The abrasive stream emerges rapidly from the blast nozzle, impacting the steel and removing surface debris, mill scale, and existing paint. It also abrades the surface, creating a fine, rough texture.
KYTC typically requires the use of a mixture of steel shot/grit. After being used, the mixture is collected and processed through a recycling machine that separates reusable shot/grit from blast wastes. The shot/grit may be used repeatedly in blasting operations until it is no longer effective and is discarded by the machine. Recycling abrasives minimizes their disposal; these wastes could negatively impact the environment if paint debris contains lead or other hazardous materials.
A few issues must be taken into account to avoid problems with dry abrasive blasting. First, it is not effective in removing invisible soluble salt contamination – it may actually embed those salts in the prepared steel substrates, resulting in the premature failure of new coatings. This can be avoided by measuring the salt contamination on the existing substrates prior to blasting and taking steps such as washing to remove those salts down to acceptable levels. During blasting, the compressor can generate water in the blast lines, which causes the blasted steel to rust before it is coated. An ink blotter can be placed at the nozzle to test the compressor’s air stream; if moisture is present, steps should be taken to eliminate it. Once the blasting operation is complete, the steel surface must undergo a visual inspection to verify it meets specified cleaning standards. Instrumentation is also used to confirm — through spot checks — that surfaces exhibit the proper texture (i.e., surface profile).
KYTC’s painting procedure consists of spraying liquid-applied inorganic and/or organic coatings onto the surface of structural steel bridge members. Multiple coats (of different coating types) are applied to achieve a proper film build and prevent missed or thin spots.
Each coat has designated functions. KYTC mandates the use of three-coat systems for paint projects. A primer, or base coat, is used to bond successive coats with the steel substrate. KYTC-approved primers contain zinc dust and provide either galvanic protection (inorganic zinc primers) or a combination of galvanic and barrier protection (organic zinc primers). Intermediate coatings typically provide barrier protection, which limits the penetration of soluble salts. These coatings incorporate organic resins and may contain metallic or platelet pigments that enhance their barrier properties. Top coats integrate organic resins that resist atmospheric degradation (i.e., weathering) caused by direct exposure to the environment (wind, rain, abrasion, and UV radiation from sunlight).
To achieve suitable coating performance, a continuous dry coating should cover all of the steel. Each layer of coating must be applied to the manufacturer-specified thickness. Once applied, a coating system should be free of visible defects (e.g., blisters, cracking, embedded debris). Using a three-coat system offers solid durability and typically results in a service life of 20 to 30 years.
All of KYTC’s bridge maintenance painting is done by contract. The contracting process can be facilitated through pre-letting site assessment in conjunction with a pre-bid conference and pre-construction conference. Proper scheduling is necessary to avoid disruptions during periods of high traffic volumes (e.g., workdays, holidays). Steel bridge maintenance painting projects are complex and typically have eight work phases:
• Mobilizing the Painting Operation,
• Deployment at the Work Site (Field Operations),
• Preparation for Waste Handling and Disposal,
• Surface Preparation,
• Monitoring Atmospheric and Surface Conditions,
• Applying Coatings,
• Inspecting Work and Affecting Repairs, and
• Demobilization.
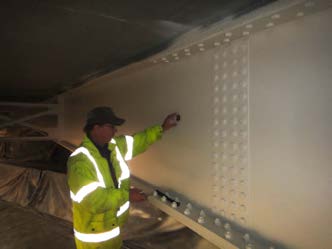
Mobilizing the Painting Operation
Ideally, a contractor’s operation arrives at a jobsite on the start date they and KYTC have agreed on. Schedule disruptions can be avoided if contractors have all the necessary equipment and materials on hand. For example, sufficient quantities of maintenance coatings should be available. Before a contractor can begin work, they must secure all mandated regulatory agency documentation and receive environmental clearances from KYTC.
Deployment at the Worksite (Field Operations)
Deployment includes all of the tasks undertaken prior to maintenance painting. These tasks are listed below. Readers should note, however, that the tasks are not necessarily performed in the order they are listed.
• Establishing traffic control (if necessary),
• Initiating painting support activities in the KYTC-approved staging area (material/equipment storage area,
coating mixing area, equipment, and vehicle parking),
• Creating a waste storage site (if necessary),
• Performing necessary site cleanup,
• Placing access equipment/devices on bridge,
• Installing necessary waste containment, and
• Establishing work areas/boundaries.
Preparation for Waste Handling and Disposal
As bridge maintenance painting generates wastes and recyclable blast residues that can potentially harm both people and the environment, they must be processed properly. Waste storage sites are established at locations determined by KYTC; EPA-compliant enclosures are built to store hazardous wastes. Waste must be kept within these enclosures, inside DOT-approved containers. Roll-offs may only be used for industrial waste (e.g., paint cans, wood forms, garbage, old containment tarps) generated during a maintenance cleaning and painting project.
Painting operations generate a flow of wastes (hazardous and non-hazardous). If lead-based coatings are removed, that waste must be treated and handled onsite as if it is a hazardous material. Dry and wet hazardous wastes are placed into containers, stored in a proper manner, and disposed of by hauling them from the jobsite to a licensed disposal facility. Approved shippers haul materials from the jobsite to the disposal facility. Paint residues are collected from containment enclosures after abrasive blasting. Interior surfaces of the blast containment enclosures must be cleaned by vacuuming when the containment is broken down or moved. Hazardous wastes are tracked via a manifesting process, while any authorized waste carrier can dispose of non-hazardous wastes. KYTC disposes of all hazardous wastes at the Doe Run Recycling Facility, which is located in Boss, Missouri.
Surface Preparation
Once the designated area has been sealed off by the containment enclosure – which captures debris produced by the blasting operation and paint overspray from the coatings application process – surface preparation begins. Prior to abrasive blasting, existing steel surfaces must be visually inspected for surface contamination (e.g., by oil and diesel fumes). Oil can be treated by solvent cleaning. Before subsequent operations can proceed, areas that were identified as contaminated with oil must be inspected to ensure they have been cleaned properly. Before structural steel surfaces undergo abrasive blasting, soluble salt (Bresle Patch) tests are often performed. If testing finds high soluble salt concentrations, they should be reduced prior to abrasive blasting. Workers are to remove all surface contamination, providing a uniform, cleanly blasted substrate of adequately roughened/ profiled steel. After workers check the blast air supply for moisture using the blotter test, abrasive blasting gets underway. Once abrasive blasting is complete, surfaces are cleaned with compressed air and waste is swept up and vacuumed from the containment area.
Operations proceed on a section-by-section basis. Each section is called a control area. Control areas are typically separated by floor beams or temporary bulkheads. Blast-cleaned areas are inspected to verify proper cleanliness using visual reference guides. Measurements are taken around the control area using instruments to confirm the proper surface profile (roughness) has been obtained. Once the contractor’s quality control (QC) inspector confirms that a proper surface profile has been obtained, KYTC’s quality assurance (QA) inspector examines and approves the work. Upon approval, a contractor proceeds to the next phase of work in the control area.
Monitoring Atmospheric & Surface Conditions
Before painting begins, workers must measure atmospheric and steel surface conditions to verify liquid coatings will not be applied to wet substrates. Rain, mist, fog, or condensation can deposit moisture on substrates. A visual inspection is typically sufficient to detect surface moisture. However, the relative humidity and surface temperature should be tested as well. Doing so helps workers avoid painting in conditions where condensation will moisten the surfaces. When substrates are moist, the applied coating does not adhere properly. Weather forecasts can indicate if rain is imminent and inform workers if they should delay painting operations. The relative humidity and surface temperature should be measured periodically to identify existing/imminent condensation threats — especially when the painting takes place at night. Because atmospheric conditions can vary at different locations on a bridge, workers are to measure humidity and temperature in the locations where painting will be done. Relative humidity and temperature measurements should be taken before and throughout the coatings application process, to ensure that conditions have not changed since the start of coatings application.
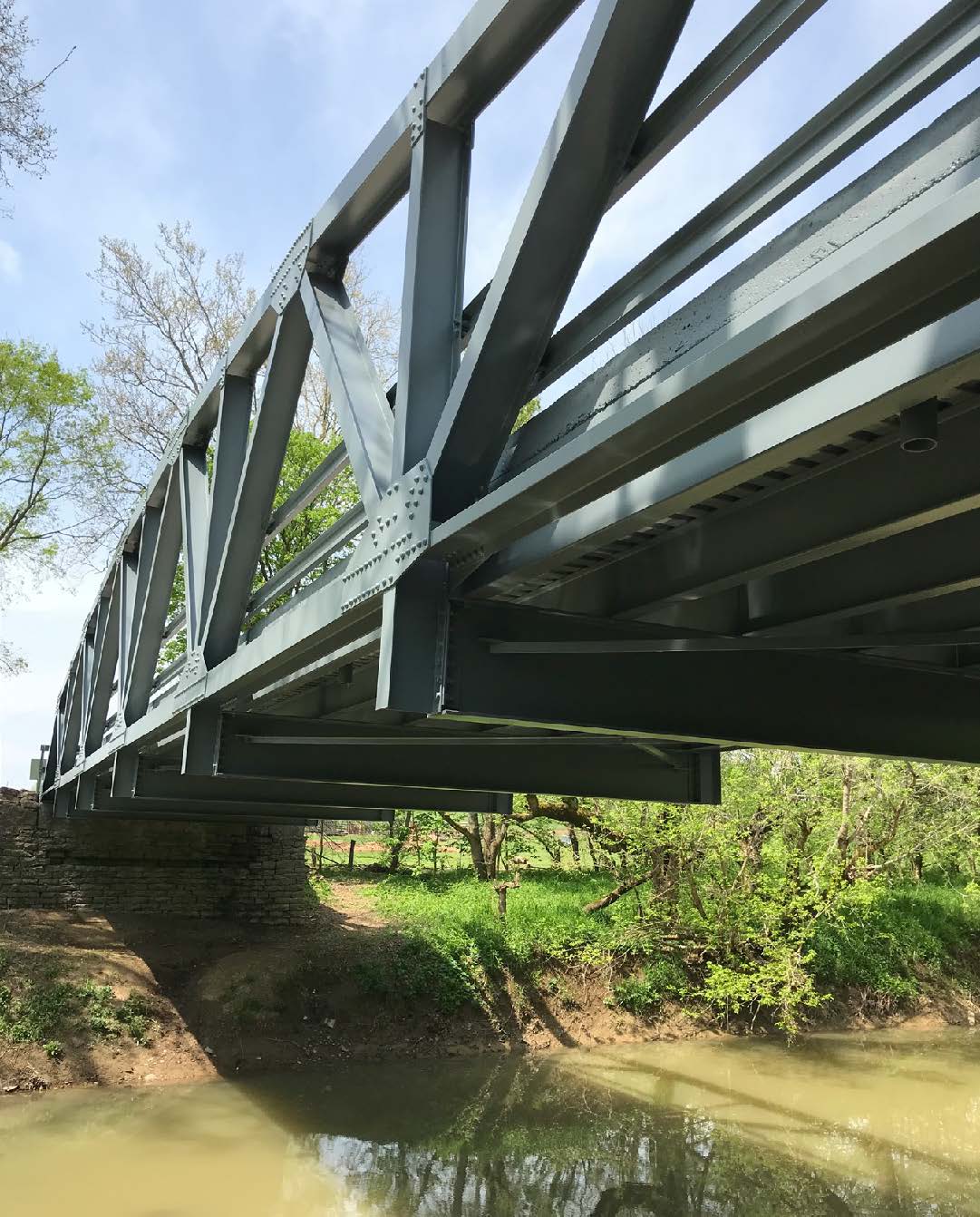
Applying Coatings
If atmospheric conditions are suitable and the blasted steel does not show signs of rust, workers can apply the coatings. Coatings are mixed and agitated according to manufacturer instructions. Workers should prepare only enough coating to cover the steel in the control area. Prepared coatings must be applied within manufacturer-specified time limits. Once preparation is complete, the coating is taken to a pump that forces it through a hose and into a spray nozzle. At the nozzle, the coating is atomized and sprayed onto the substrate. Each coat must cure according to manufacturer directions before the next coat is applied.
The primer is applied first. Once the primer cures and is inspected and approved, workers apply successive coats. When applying the wet coating, workers can use wet film gauges to measure the coating thickness. Measuring coating thickness during the application process helps to ensure that when the coating dries it will have manufacturer-specified thickness. Following the application and curing of each coat, the contractor’s QC inspector visually inspects the dried coating to detect flaws. Any flaws must be repaired before successive coats are applied. The contractor’s QC inspector also measures dry film thickness to verify the proper film build has been achieved. After KYTC’s QA inspector approves the work, painters complete the coating application phase of work.
Inspecting Work and Effecting Repairs
Once KYTC’s QA inspector approves the painting work, the Division of Construction’s chief coatings inspector performs a final site inspection. The chief coatings inspector reviews the coating work and notes deficiencies that require corrective action (e.g., paint flaws, overspray on concrete, paint spills on the ground, bulkhead misses, rigging scrapes). Contractors correct deficiencies before containment and access rigging is removed. KYTC’s chief coatings inspector will examine remedial work, in consultation with the contractor, to verify its satisfactory completion.
Demobilization
Contractors remove work-related materials/wastes from the jobsite before leaving. They remove all waste storage enclosures once any waste and/or paint residues are taken for disposal/recycling. Waste found on the ground must be collected and disposed of in the proper manner. Traffic signs must be removed. If the surrounding environs have been disturbed, that disturbance must be remediated before a contractor departs the jobsite. A contractor must leave the jobsite in the same condition it was in before maintenance painting began.
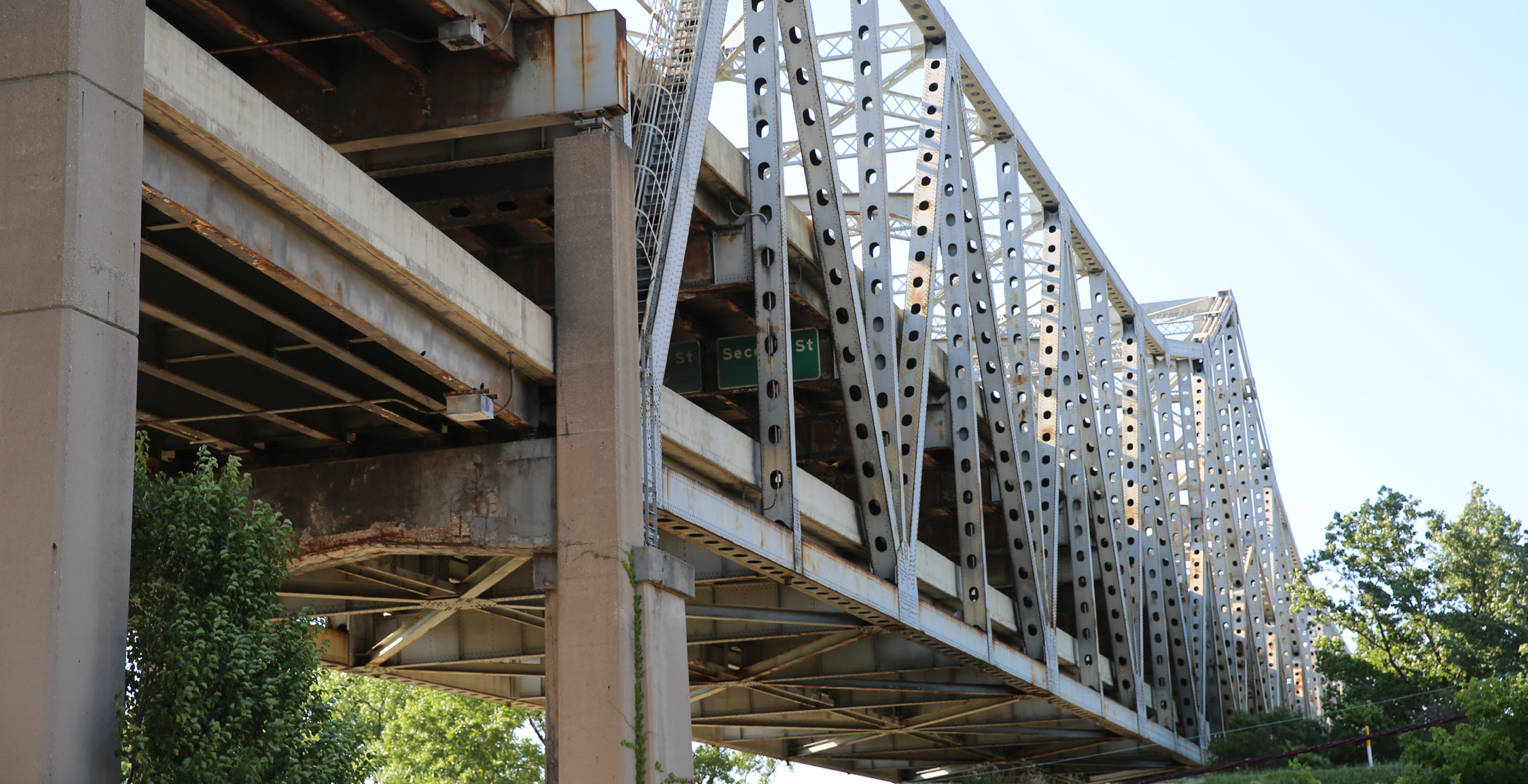
Inventory
KYTC conducts maintenance painting on steel bridges it owns as well as bridges owned by other jurisdictions. While the primary painting inventory is the Kentucky-owned group (structures designated with a “B” within the KYTC BrM database), various agreements or policies may include bridges from county, city, parks, railroad, or adjoining state inventories. KYTC is responsible for painting most of the bridges that connect to adjoining states; border state maintenance agreements are developed to fund these major projects.
KYTC’s inventory of steel bridges specifies bridge type (e.g., multi-girder, non-redundant girder, pony truss, thru truss, deck truss, suspension, cable stay). Bridge type significantly impacts the complexity — and cost — of a painting project. The inventory also specifies the location of each bridge. Data are provided on latitude, longitude, stream crossed, route, intersecting route, and county. This information is important for programming maintenance activities as grouping bridges helps KYTC achieve economies of scale and improve project management.
Other useful information in the inventory includes vertical clearance, existing coating type, steel surface (mill scale), and condition of the existing coating. Data pertaining to coating condition should note the following: failure mechanism (corrosion, steel disbondment, chalking, inter-coat adhesion), failure location (beam-ends, fascia, general), and degree of failure (approximate percentage of area).
Programming
Employees developing and programming bridge maintenance activities must have knowledge of the funding sources which can underwrite their maintenance painting budget. Funding sources include:
• Maintenance (FE02) Budget,
• 6-Year Highway Plan, Special Projects, and
• End of Fiscal Year Adjustments.
Several factors influence the scope of the bridge painting program, including the available budget, project complexity, and market conditions (i.e., amount of work in the region). When making decisions about the program, the Specifier/Programmer also considers:
• Scheduling (spreading the work over various construction lettings),
• Contract administration (coordinating with the Division of Construction),
• Projects requiring extended development (e.g., railroads), and
• Project time requirements (e.g., multi-season projects, completion dates, other projects).
Other considerations when developing the bridge painting program include:
• Disturbing lead on bridges (e.g., remove/replace or encapsulate),
• Leaded residues (to be recycled or sent to an appropriate waste facility),
• Distributing funding across KYTC districts,
• Reciprocal agreements with other bridge owners (e.g., states, cities, parks,), and
• Including rehab and/or repair work.
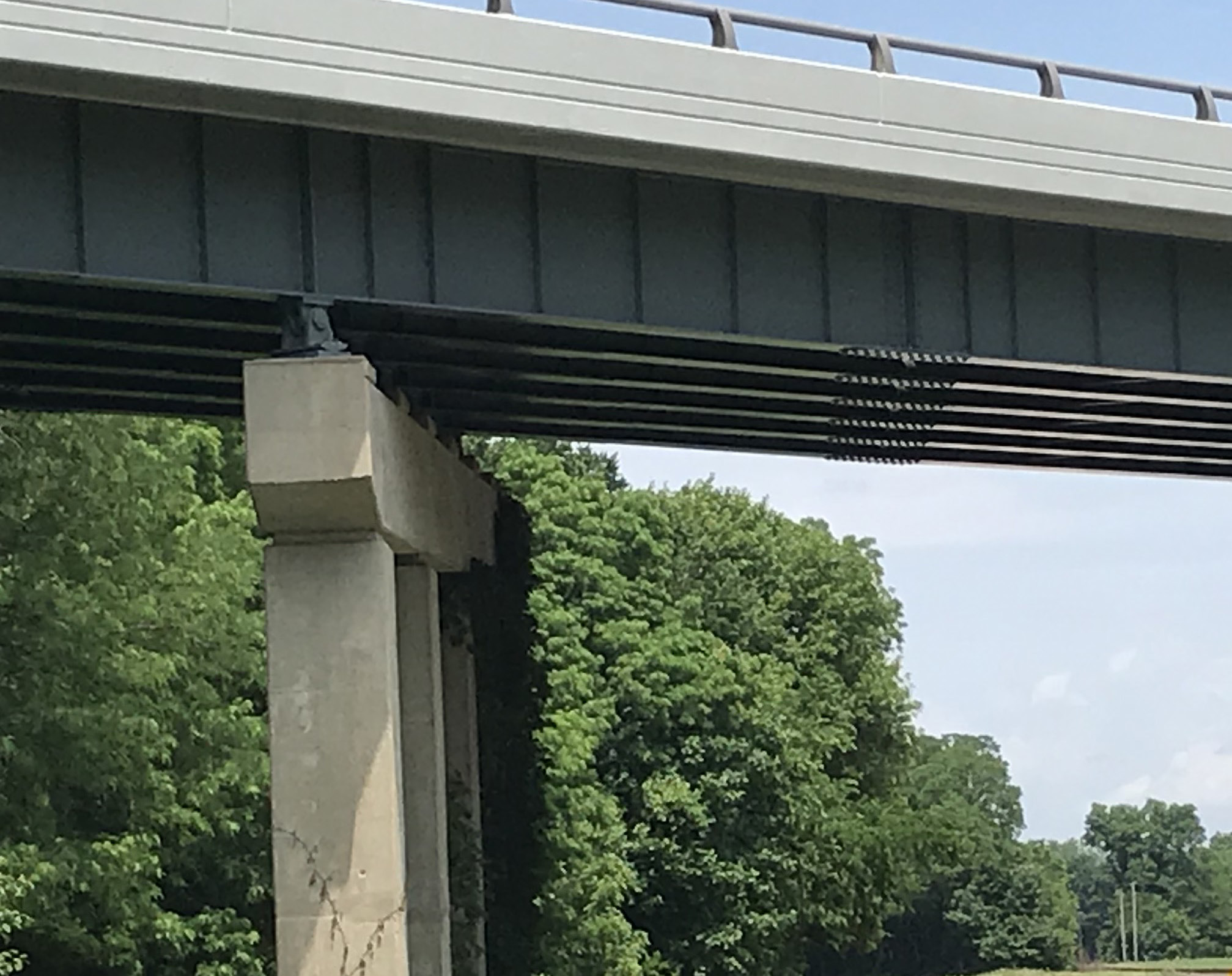
Historically, KYTC has adopted a continuous improvement approach, whereby newly developed materials and/or methods are incorporated into the painting program so that projects are completed in the most cost-effective manner possible.
As part of the bridge painting program individual bridge painting proposals go to letting. Proposals often encompass several smaller bridges. However, proposals for large bridges (e.g., Ohio River bridges) are usually limited to a single bridge or pair of bridges. When developing a bid proposal package for cleaning and painting projects, it is important to bear in mind that each bridge is unique. Some of the variables that may be included in proposals are:
• Construction details,
• Steel condition,
• Coating condition,
• Presence of heavy metals,
• Protected habitats,
• Protected waters,
• Temporary traffic control issues,
• Sensitive environmental receptors,
• Worker access issues, and
• Oversize loads (e.g., farm equipment).
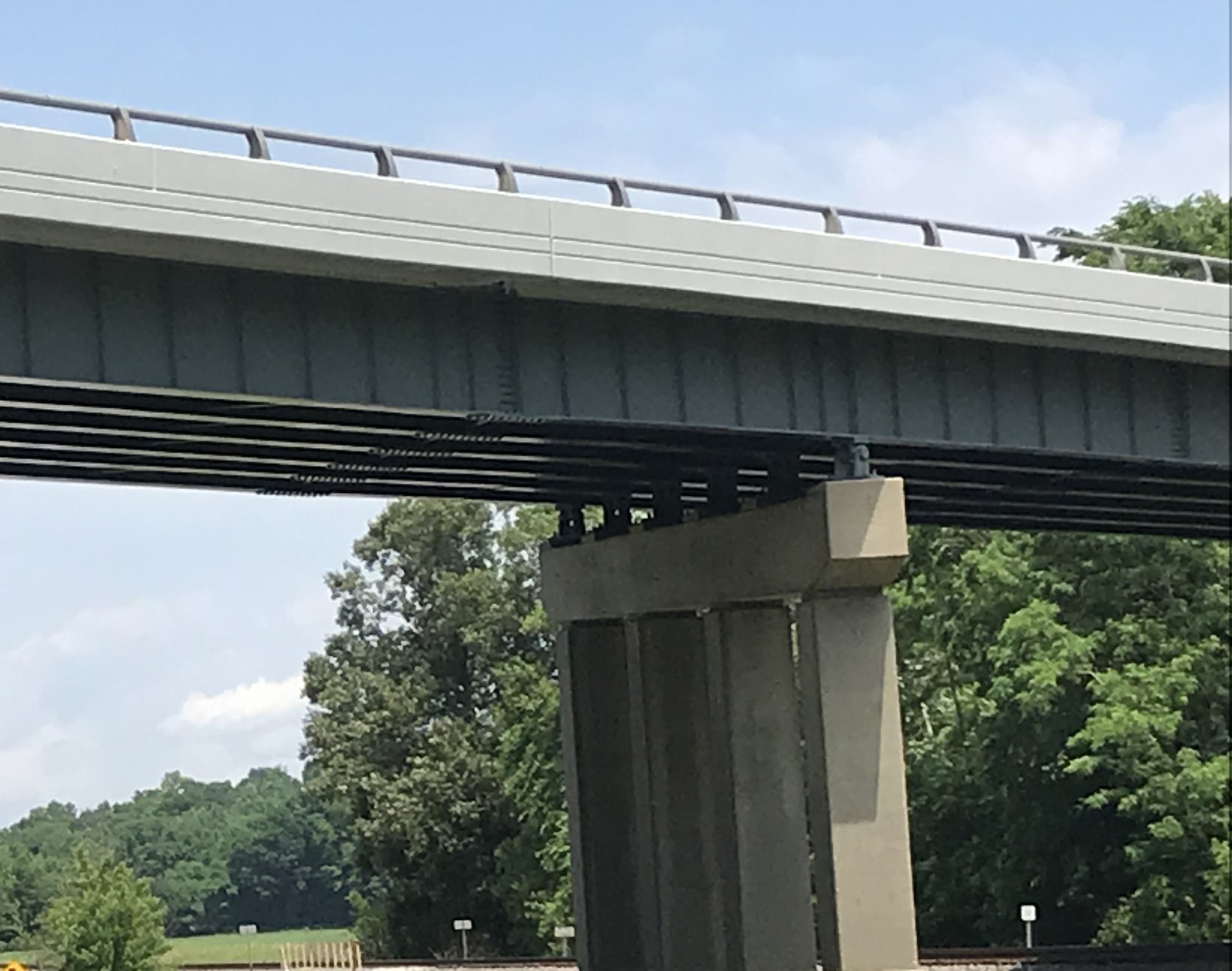
While biennial inspection data (i.e., Structure Inventory and Appraisal [SI&A]) provide some of this information, the individual developing a proposal should conduct an onsite visit to fully understand site conditions.
Helpful resources include:
• KYTC Standard Specifications for Road and Bridge Construction
• KYTC Standard Drawings
• KYTC List of Approved Materials
• KYTC Work Zone Safety Policy
• FHWA Manual on Uniform Traffic Control Devices (MUTCD)
• Other Industry Standards and Guides
KYTC maintains a list of prequalified bridge painting contractors. The bridge coatings industry has certifications for contractors and trades (e.g., coatings inspectors) which can be referenced to improve the quality of work.
While these resources are critical for developing a proposal-type bid package, Special Notes are the principal component. These notes address the unique characteristics of each bridge and specify a bridge’s location. Special Notes provide detailed explanations the specific requirements for cleaning and painting a bridge.
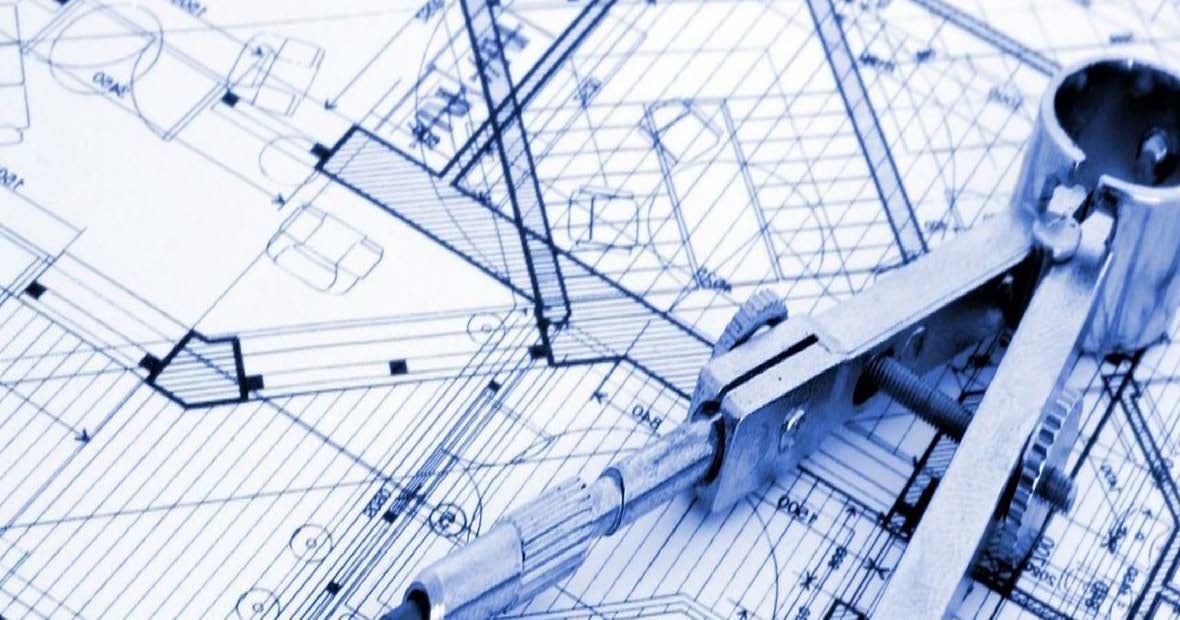
• Kentucky Standard Specifications for Road and Bridge Construction
o Section 100, General Provisions
o Section 614, Maintenance Cleaning and Painting Steel Bridges
o Section 821, Structural Steel Coatings
• KYTC Bridge Inspection Procedures Manual
o Section 200, Inventory
o Section 300, Inspection
• KYTC Field Operations Guide (FOG)
o Section 812, Repairing Steel Bridge Members
• KYTC Maintenance Manual (MAIN)
o Section 806, Bridge Maintenance/Selection of Paint Color
o Section 808, Bridge Maintenance/Cleaning & Painting of Steel Structures
• KYTC Construction Manual (CST)
o Section 1314, Bridge Painting
• KYTC Structural Design Manual (SD)
o Section 501-3, Bridge Superstructure/Structural Steel
• Kentucky Methods Guidance Manual (KM)
o KM 64-256-08, Resistance Testing of Structural Steel Coatings to Methyl Ethyl Ketone
o KM 64-258-08, Measurement and Acceptance of Film Thickness of Structural Steel Coatings
o KM 64-263-08, Test Method for Analysis of Calcium Sulfonate
o KM 64-266-08, Performance Based Evaluation and Acceptance of Structural Steel Coating Systems
• KYTC Materials Field Sampling Manual (MFS)
o Section 522, Materials Field Sampling/Chemistry/Structural Steel Coatings
• KYTC Division of Materials Manual (MAT)
o List of Approved Materials (LAM), Structural Steel Coating Systems, Class II (Type I and Type II)
o Section 403, Materials/Structural Materials Branch/Chemical Section
American Society for Testing Materials, ASTM D4285-83(2018), Standard Test Method for Indicating Oil or Water in Compressed Air, ASTM International, West Conshohocken, PA, 2018
American Society for Testing Materials, ASTM D4417-14, Standard Test Methods for Field Measurement of Surface Profile of Blast Cleaned Steel, ASTM International, West Conshohocken, PA, 2014
Kentucky Administrative Regulations, 401 KAR 32:010, General Provisions for Hazardous Wastes
Kentucky Administrative Regulations, 401 KAR 32:020, Manifest System
Kentucky Administrative Regulations, 401 KAR 32:030, Pretransport Requirements
Kentucky Administrative Regulations, 401 KAR 35:180, Use and Management of Containers (Interim Status)
National Association of Coatings Engineers and Society for Protective Coatings, Joint Standard, NACE No. 2/SSPC-SP 10-2006, Near White Metal Blast Cleaning ISBN: 1-57590-108-0
NACE (National Association of Corrosion Engineers), Coating Inspector Program Level 1
The Society for Protective Coatings, SSPC Solvent Cleaning Guide
The Society for Protective Coatings, SSPC – Guide 6, Guide for Containing Surface Preparation Debris
The Society for Protective Coatings, SSPC – AB 2 Cleanliness of Recycled Ferrous Metallic Abrasive
The Society for Protective Coatings, SSPC – C3 Lead/Hazardous Coating Removal
The Society for Protective Coatings, SSPC – Bridge Coating Inspector Program (BCI) Level 1
US Code of Federal Regulations, Title 29, Occupational Safety and Health Administration (U.S.) – Department of Labor (U.S.) 29CFR 1926 Safety and Health Regulations for Construction ISBN: 978-0-16092-897-0
US Code of Federal Regulations, Title 49, Transportation, Pt. 100-177, Revised as of October 1, 2015. 49CFR172.301 and 49CFR172.302 General marking requirements for non-bulk packagings ISBN: 978-0-16093-074-4
US Code of Federal Regulations, Title 49, Transportation, Pt. 100-177, Revised as of October 1, 2015. 49CFR173.213 Non-bulk packagings for solid hazardous materials in Packing Group III ISBN: 978-0-16093-074-4
US Code of Federal Regulations, Title 49, Transportation, Pt. 100-177, Revised as of October 1, 2015. 49CFR173.240 Bulk packagings for certain low hazard solid materials ISBN: 978-0-16093-074-4
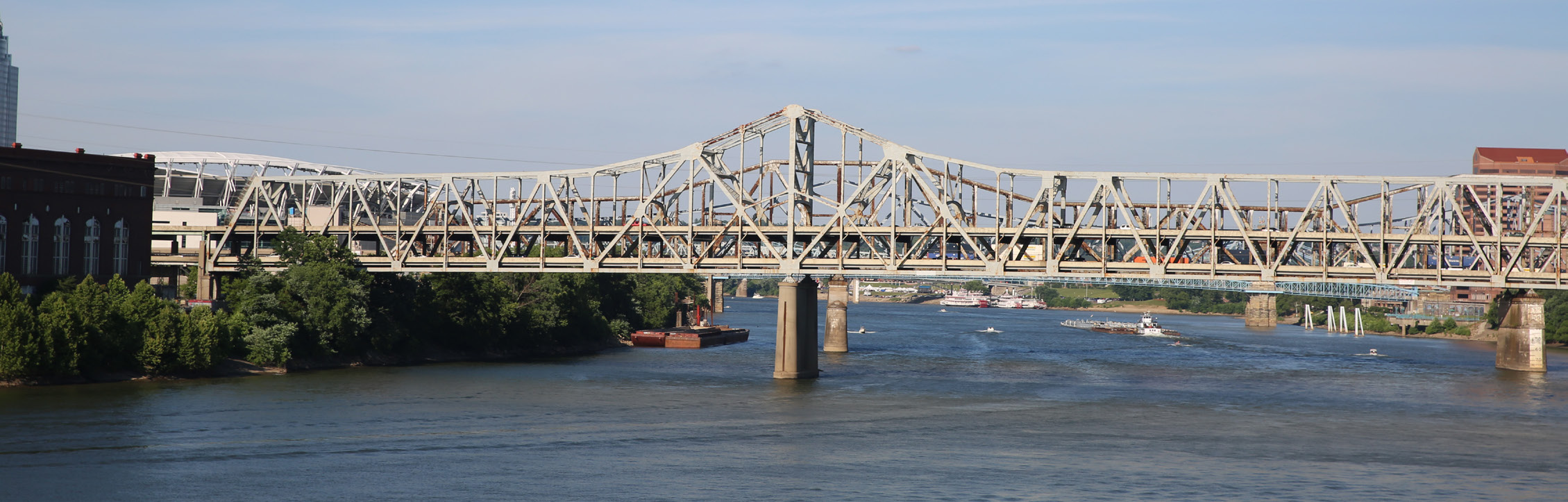